Walls aren't always straight!
- Survey Team
- Aug 19, 2024
- 3 min read
The plans are not always accurately representing real life.
In real life, walls are not perfect 90 degrees; they could be 90.03, 91, or even 89.97 degrees.
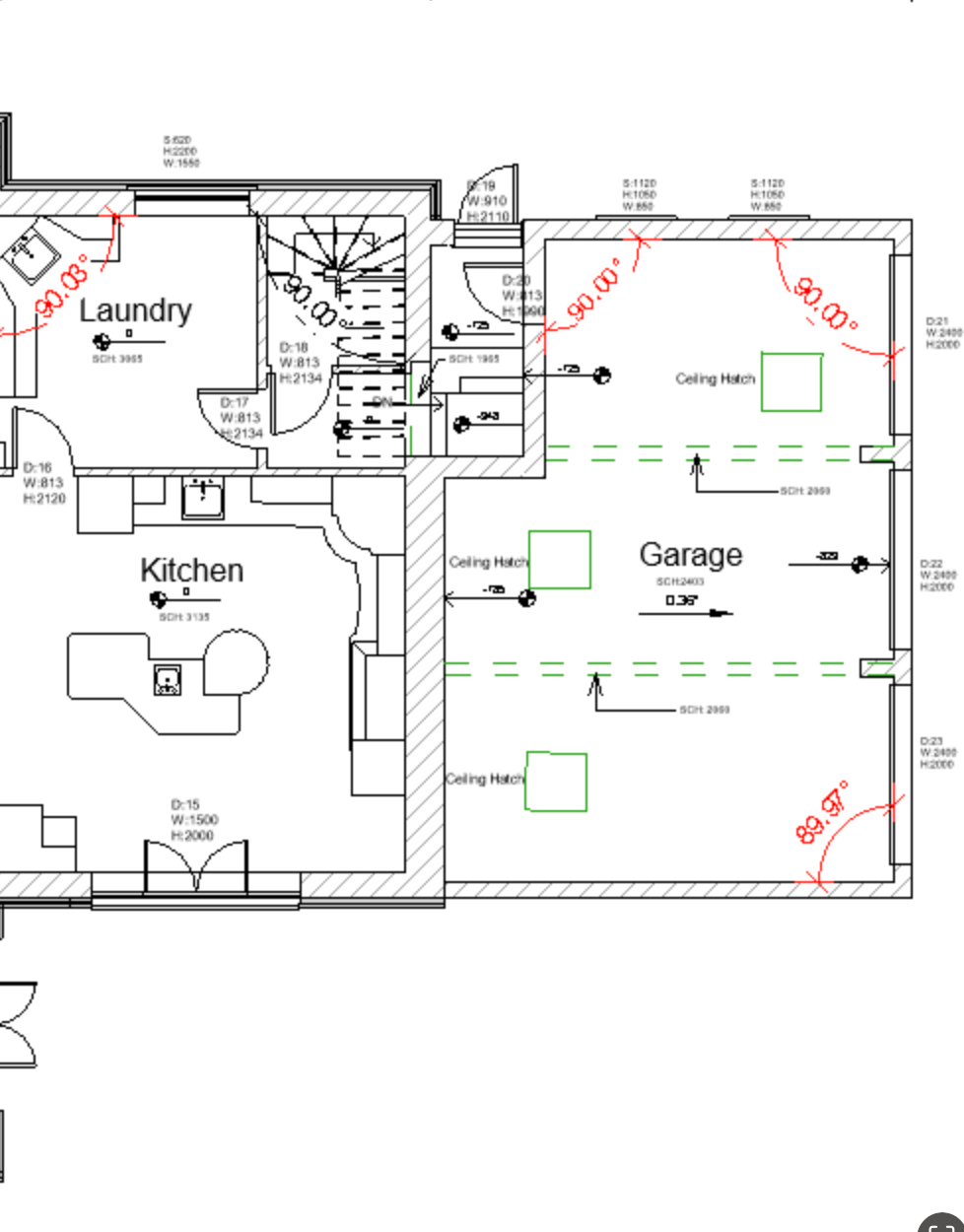
Houses settle over time, the walls, floor, ceilings shift or lean slightly in or out. These changes might go unnoticed to the naked eye or even when measuring by hand. That's why for large developments lasers scanning is the only option.
Laser scan data can pick up these small details. But this level of accuracy is rarely used is small projects!
The closer to the scan data we look the more we see that walls, floor ceilings may not appear perfectly straight. Instead, they might be curved like gentle waves or even show as double lines, revealing the inaccuracies of the surfaces and angles.
This is especially confusing in 2D deliverables like DWG and PDF drawings but less confusing in 3D models see below

The same area in a 3D model clearly explains exactly these inaccuracies when 2D drawings are limited in explaining these changes with just lines. And this level of precision when working only with 2D drawings can just do the opposite cause confusion in the design and planing process.


For this reason the practice of displaying walls as straight lines and angles are implemented when working with scan data and averaged to fit the 90 degrees. Unless requested by client to follow the true shapes where walls and angles may not be straight.
We at SpaceSurvey produce measured house drawings in 2D drawings and/or 3D models for coordination purpose (That are not intended for manufacturing purposes i.e. windows, kitchens, wardrobes etc...), unless requested for manufacturing purposes.
Note: But we just can't go and average everything or we will end up in the other side of the road in a ditch again.
So structural changes +/- 3cm where noticed in quality control or modelling process are significant enough for us to advise the clients and ask for advice if they want to display them as they are or average this.
If there is not clarity on this. always discuss with your architect the intended use of the measured house survey.
Although many prefer to go with the flow and book something and think later due to time restrictions or DIY to save money, this is not ideal.
Two reasons why:
If custom furniture has been created that doesn't fit, it my have to be reordered for a delivery in another 4 weeks <-- Real case.
Due to not having the right planing as the application has been rejected, the loan from the bank is not given and the bridging loan is coming to an end. This has burned all the cash in the development, whiles resubmitting the application. <-- Real case.
Conclusion:
It is important that you communicate your expectations clearly, to get the correct plans for the correct purpose the first time.
Unless the plans are made for manufacturing purposes ask the supplier/installer to visit the site and carry out their own survey suitable for the intended purposes.
Where plans for manufacturing purposes are needed just let the surveyor know before the work is done.
Or if we worked on this project and have the scan data and your planing to make any orders of custom made furniture please let us know and we can check the dimensions of that particular area against the scan data to save your time.
Peter Bauman
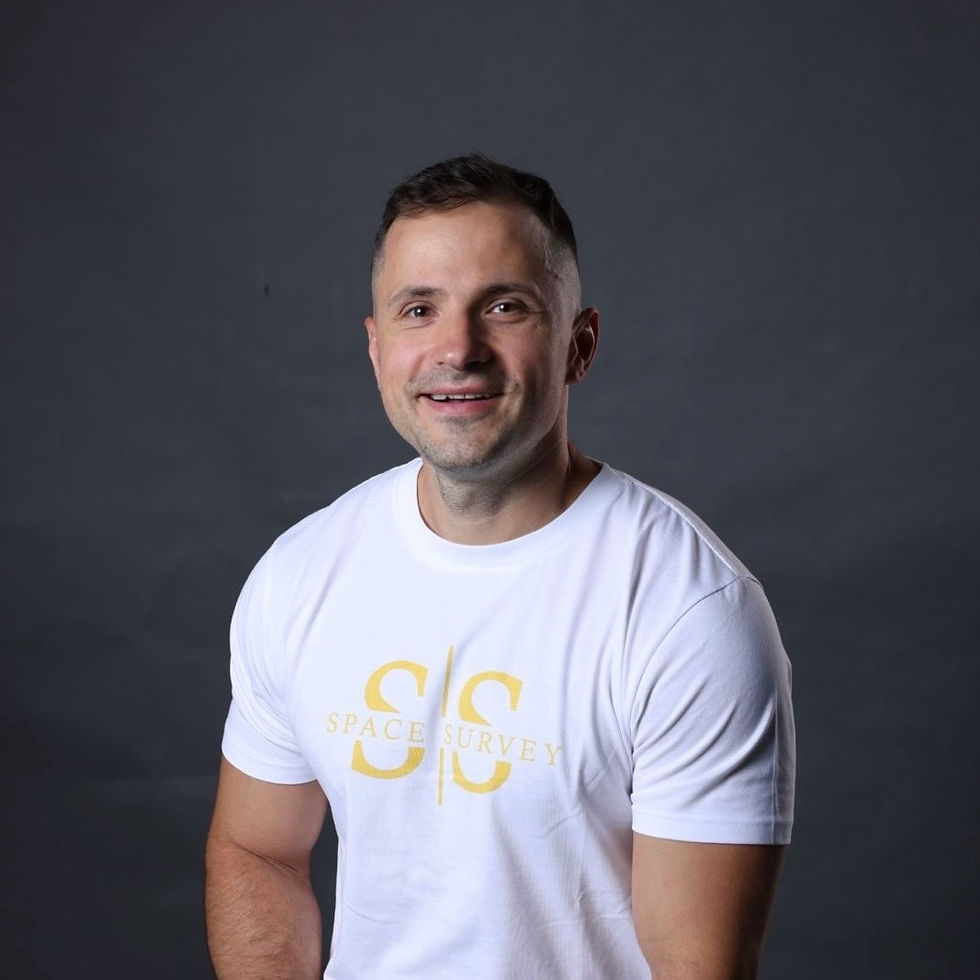
Comments